El proyecto HYBRIS tiene como objetivo desarrollar un sistema híbrido de almacenamiento de energía (HESS) para conectarse a la red de corriente alterna (CA). El HESS cuenta con dos tecnologías de batería: baterías de óxido de titanio y litio (LTO) y baterías de flujo redox orgánico acuoso (AORF). La tecnología LTO se caracteriza por capacidades de alta potencia; es decir, puede proporcionar una respuesta rápida cuando se requiere una demanda de alta potencia. Sin embargo, LTO sufre de capacidades de almacenamiento de energía reducidas. Por otro lado, AORF presenta una alta capacidad de energía, un costo reducido y un mantenimiento simple, pero su eficiencia de almacenamiento de energía disminuye considerablemente en la operación de alta potencia.
La unión de ambas tecnologías de batería en un sistema híbrido permite alcanzar valores arbitrarios de capacidad energética y potencia nominal simplemente combinando diferentes proporciones de ambas tecnologías de batería, proporcionando así flexibilidad en el dimensionamiento del sistema de almacenamiento. Esto permite un tamaño y costo reducidos, en comparación con el mismo sistema pero empleando solo una de las tecnologías de batería. Además, permite que la batería AORF funcione con la máxima eficiencia, rentabilizando la inversión realizada en el sistema híbrido y haciéndolo más sostenible.
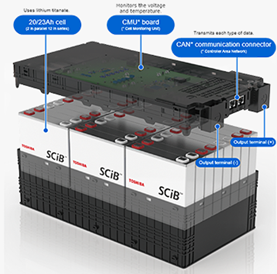
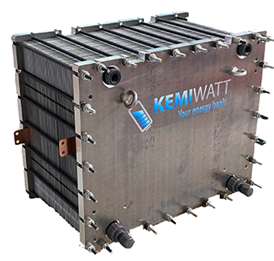
Una pieza clave para posibilitar la hibridación del sistema es el sistema de conversión de potencia (PCS). Tanto las baterías LTO como las AORF proporcionan la energía en corriente continua (CC), pero la energía debe suministrarse u obtenerse de la red en forma de CA. Los convertidores de potencia permiten convertir la energía eléctrica de CC a CA y viceversa, posibilitando la transferencia de energía de las baterías a la red, de la red a las baterías e incluso entre baterías. La configuración interna del PCS se puede concebir empleando diferentes tipos y números de convertidores, distribuyendo la potencia entre múltiples convertidores operando en paralelo, y con una amplia variedad de componentes a elegir para concebir los convertidores.
El principio de operación de los convertidores consiste en emplear elementos magnéticos y capacitores (dispositivos pasivos) para almacenar momentáneamente la energía de la entrada y luego entregarla a la salida en el modo de corriente y voltaje requerido. Para conectar/desconectar estos elementos hacia/desde los puertos del convertidor, se emplean dispositivos semiconductores de potencia (dispositivos activos), por ejemplo, transistores y diodos. Este ciclo se repite decenas de miles de veces por segundo, por lo que la capacidad de almacenamiento de energía de los dispositivos pasivos puede reducirse considerablemente, permitiendo convertidores muy compactos. En este marco, los socios de HYBRIS, IREC y CEA, han estudiado múltiples configuraciones con el objetivo de realizar una optimización multiobjetivo. Las configuraciones consideradas, también conocidas como arquitecturas de conversión, se muestran en la Figura 2. Ambas baterías requieren un convertidor CC-CC previo al convertidor CC-CA para aumentar el voltaje a un valor adecuado, alrededor de 800 V. Luego, el convertidor CC-CA puede transferir energía correctamente hacia y desde la red CA. Las baterías están acopladas a la red de ca (arquitecturas A y C) o después de los convertidores dc-dc (arquitecturas B y D). También consideramos hasta tres convertidores dc-dc operando en paralelo para distribuir las pérdidas de conversión y reducir la temperatura de los componentes (arquitecturas A y B).
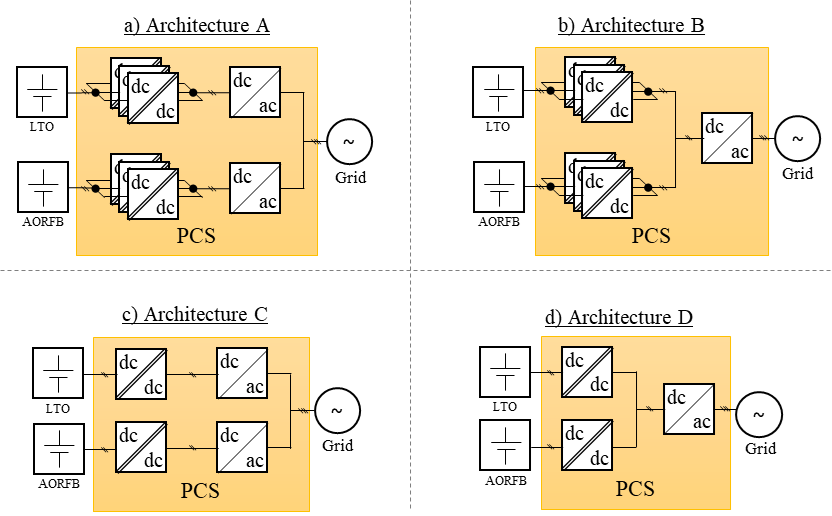
El estudio de optimización tiene los siguientes objetivos:
- Minimización de las pérdidas de energía del PCS (P loss). Un convertidor de energía ideal tendría cero pérdidas de energía, de modo que la misma cantidad de energía proveniente de la entrada se entrega a la salida; es decir, una eficiencia de conversión del 100%. Sin embargo, debido a múltiples procesos físicos, parte de la energía procesada se pierde, alcanzando generalmente valores de eficiencia entre el 90% y el 99%. Calculamos las pérdidas en los convertidores a través de modelos electrotérmicos completos de los diferentes componentes y los datos disponibles en las hojas de datos de los componentes.
- Minimización del costo de capital de PCS ( C capital). Los componentes que componen los convertidores de potencia tienen un coste de material y fabricación que debe ser considerado. La suma de ambos conceptos define el costo de capital del PCS. Hemos obtenido el costo de cada tipo de componente (semiconductores, capacitores, conductores de cobre, etc.) de la literatura y proveedores de componentes para cantidades de pedido en el rango de decenas de miles de unidades, lo que representa economías de escala. Luego, el valor del costo se modela en función de los parámetros constructivos de los componentes, es decir, el área del semiconductor, el peso del conductor de cobre, el volumen del disipador de calor, etc.
- Minimización del coste derivado de la fiabilidad PCS (C reliability). La fiabilidad del PCS, es decir, la probabilidad de que no falle en un momento dado, depende de la dureza de su funcionamiento. Por ejemplo, cuanto mayor sea la temperatura de funcionamiento de los componentes, más probable será que fallen y menor será su fiabilidad. Además, cuanto mayor sea el número de convertidores, es más probable que uno de ellos falle. Una falla de un componente dado en un convertidor generalmente conduce al apagado del convertidor y, en algunos casos, de todo el PCS. Traducimos la confiabilidad al costo al considerar el costo de reparación y la pérdida de ingresos debido al tiempo de apagado parcial o completo del sistema. Calculamos la confiabilidad del sistema a través del método matemático de las cadenas de Markov y los datos de confiabilidad de los componentes disponibles en la literatura.
Definimos el problema de optimización con la siguiente función objetivo:
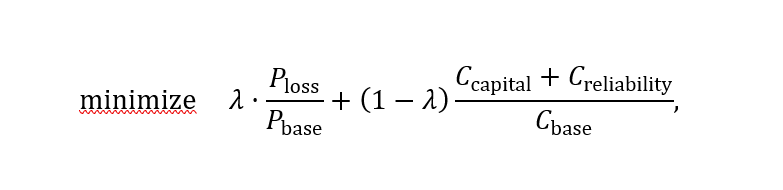
donde las variables P loss, C capital y C reliability son una función de los siguientes parámetros:
- Los componentes comerciales utilizados en cada convertidor.
- La configuración de los componentes magnéticos en cada convertidor.
- Los parámetros de operación de los convertidores.
- El tamaño de los disipadores de calor conectados a los dispositivos semiconductores.
Además, el problema de optimización está sujeto a varias restricciones, siendo las más relevantes:
- Los componentes no pueden superar una temperatura máxima determinada.
- Los dispositivos semiconductores deben caber en el área de montaje disponible de los disipadores de calor.
- En los elementos magnéticos, los devanados de cobre deben caber dentro del espacio de devanado disponible del núcleo magnético.
- El campo magnético a través de los núcleos magnéticos no puede superar el valor especificado por el fabricante.
- La distorsión de las corrientes de red a la potencia nominal de operación no puede ser superior al 10%.
Los parámetros P base y C base permiten normalizar las pérdidas y costes de forma que ambos objetivos sean comparables. Sus valores están fijados en 1000 W y 1000 €, respectivamente. El parámetro λ permite o bien priorizar la minimización de las pérdidas o bien el coste. Por ejemplo, λ=1 minimiza solo las pérdidas, mientras que λ=0 hace lo mismo pero a costo.
Usamos un solver de optimización de MATLAB®para resolver el problema, ejecutándolo para cada arquitectura y para tres valores del parámetro λ, priorizando costo (λ=0.2), pérdidas (λ=0.8) y dando igual prioridad a ambos (λ=0.5 ). El solucionador genera muchas soluciones viables de la configuración PCS que cumplen con las restricciones establecidas. La Figura 4 muestra la nube de soluciones para las cuatro arquitecturas. En la figura, cuanto más cerca está una solución dada del origen de los ejes, menor es la función objetivo y, por lo tanto, mejor es el resultado. Las soluciones en la frontera de las nubes de puntos en la Figura 4 definen el llamado frente de Pareto (líneas discontinuas en la Figura 4). Una solución dada es parte del frente de Pareto si no hay soluciones alternativas que mejoren uno de los objetivos, por ejemplo, el costo, sin empeorar los otros objetivos. De esta forma, el frente de Pareto permite identificar las compensaciones existentes del sistema. En el presente caso, en las cuatro arquitecturas, el PCS presenta un claro compromiso entre pérdidas y costo. Por ejemplo, podemos aumentar la sección transversal de los conductores de cobre en los elementos magnéticos para reducir las pérdidas, pero esto será a expensas de un mayor costo. En los extremos del frente de Pareto, una pequeña mejora en uno de los objetivos conlleva una gran agravación del objetivo complementario. Por lo tanto, existe un valor mínimo alcanzable del costo y las pérdidas del PCS. La figura 4 también revela que las arquitecturas PCS con un menor número de convertidores logran pérdidas y costos generales más bajos.
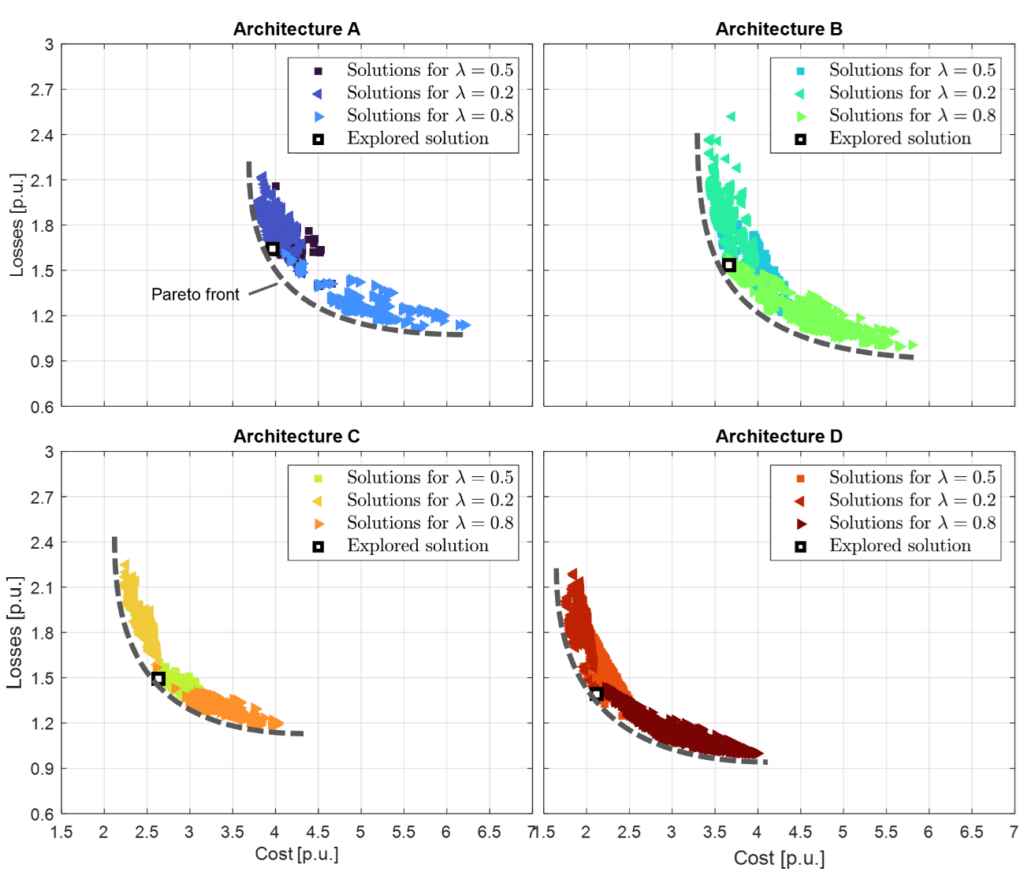
Para cada arquitectura, exploremos en detalle una solución representativa, marcada con un cuadrado blanco y negro en la Figura 3. La Figura 5 desglosa las pérdidas y el costo entre los componentes y conceptos relevantes del PCS para cada solución seleccionada. En la Figura 5 podemos ver que los PCS que cuentan con un convertidor dc-ac para cada batería (arquitecturas A y C) presentan pérdidas magnéticas proporcionalmente más altas y pérdidas de semiconductores más bajas que las arquitecturas con un solo convertidor de CC-CA (arquitecturas B y D). La reducción del número de convertidores dc-dc paralelos conduce a una reducción de las pérdidas magnéticas, mientras que las pérdidas de los semiconductores apenas se ven afectadas. Considerando la potencia nominal del PCS (59 kW), las eficiencias de conversión son del 97,2%, 97,4%, 97,5% y 97,6% en las arquitecturas A, B, C y D, respectivamente.
La Figura 5 muestra que, en todos los casos, los semiconductores representan casi el 50 % del costo del sistema. El segundo costo de capital más grande son los elementos magnéticos, seguidos de cerca por el costo de reparación, el costo del sistema de enfriamiento (disipadores de calor más ventiladores) y el costo de los condensadores. El costo de los componentes auxiliares y la penalización de costos por pérdidas de ingresos son marginales en todos los casos (≤ 6%). En general, las Arquitecturas C y D presentan costos de materiales más bajos. Aunque existe cierta dependencia lineal del costo de cada componente con su potencia nominal, resistencia térmica, etc., aún existe un costo fijo en forma de costo del paquete, costo de fabricación, componentes auxiliares, etc. Por lo tanto, cuanto mayor sea el número de componentes en una arquitectura, mayor será el costo del sistema.
En conclusión, para el presente HESS, la arquitectura PCS con un único convertidor CC-CC por batería y un único convertidor CC-CA (arquitectura D) se presenta como la solución óptima, con la mejor compensación entre costo y eficiencia. Vale la pena señalar que si consideramos mayores penalizaciones por pérdida de ingresos por el apagado del sistema inducido por fallas, las arquitecturas con un mayor grado de paralelización pueden volverse competitivas en costos. Además, la arquitectura óptima puede ser diferente si la potencia nominal del sistema es sustancialmente menor o mayor. En los próximos meses, los socios IREC y CEA trabajarán juntos para construir un demostrador de bajo consumo para validar el HESS PCS óptimo.
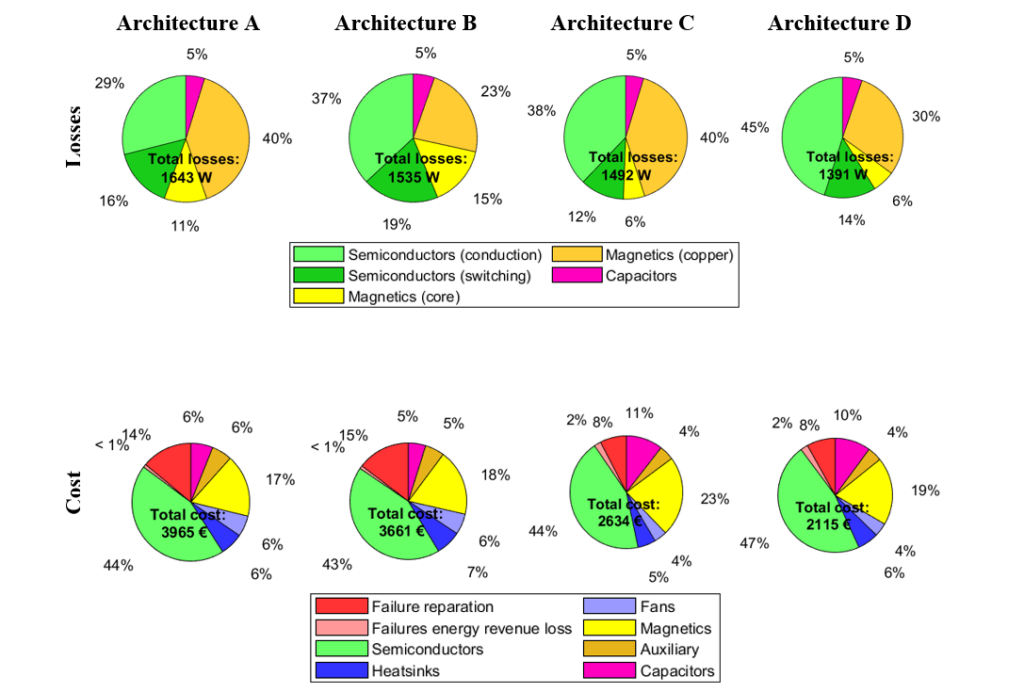
Escrito por Àlber Filbà, Oriol Esquius, Lluís Trilla, Clàudia Cabré i José Luís Domínguez, del IREC.